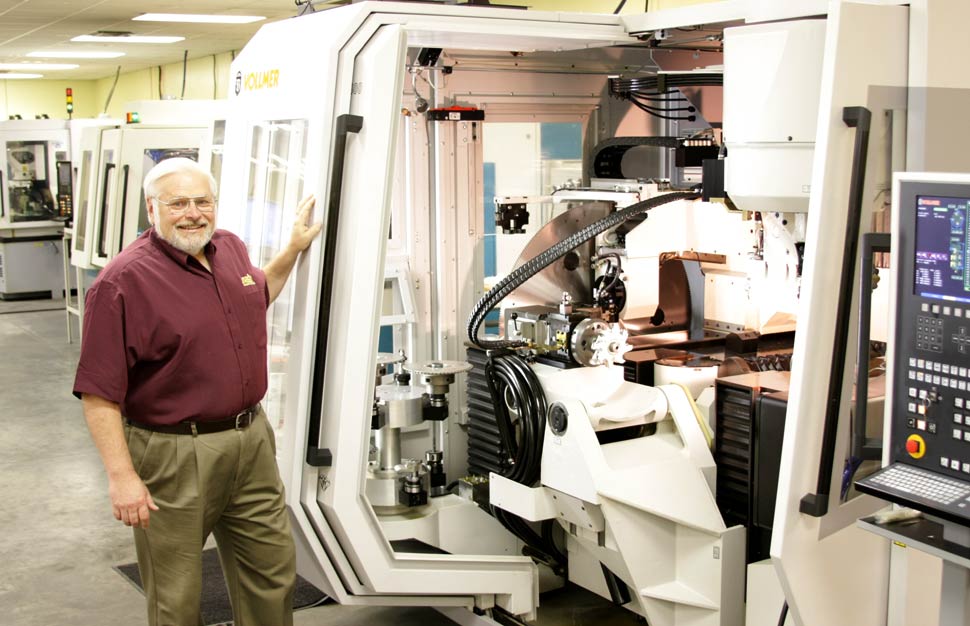
Dave Freund standing in front of one of the QXD400's in the newest Saber Production Cell dedicated to 24x7 continuous production
Wood Without Trees
Using PCD for Woodworking has "Branched" Out...
"Wood" Without Trees
by David G. Freund, President
Saber Diamond Tools, Inc.
The concept of manufacturing products from wood is not new. In fact, wood was probably the very first raw material used in any manufacturing process. From the first caveman who pushed a sharp stone
through a tree branch to create an ax, our civilization has been into woodworking of some type. Over the last several thousand years, this wood processing has continued to be improved and refined. Instead of doing things by hand, machines have taken over
most of the tasks. Manufacturing items from wood has become faster and more accurate. As this manufacturing process has evolved, so has the tooling.
Wood has been a construction material since the very earliest times. When it comes to manufacturing items out of wood, you would think a very simple tool could do the job without any problem. One of the reasons wood has been used for so long is that it is
relatively easy to cut. A sharp stone, soft metal or even a good set of dentures will do the job! Cutting wood is not nearly as difficult as cutting tungsten carbide, concrete or granite. All of these are hard materials; so it makes sense that you need something
even harder, like diamond, to penetrate them. So why then would diamond, the hardest material on earth, become a popular tooling choice to cut wood, which is one of the softest materials? You have to scratch your head to figure out the logic.
To understand why Polycrystalline Diamond (PCD) is used to cut wood, you have to forget about what is being cut and concentrate on how it is being cut. The speed and accuracy that is needed in the manufacturing process of today is what forces the
use of diamond. While carbide is measured in cubic millimeters of material removed and we evaluate stone and concrete cutting in terms of inches per minute feed rates, woodworking is discussed in terms of cubic yards per minute of material removed and
thousands of feet per minute feed rates. Think about it! Wood is processed at up to 2500 feet per minute, that's 30 miles per hour!!! In one afternoon you could cut a board, one inch thick from Vancouver to Seattle. In roughly five days, you could cut your
way from Vancouver to Miami. This is tremendously fast cutting but it also has to be combined with accuracy and high quality.
The accuracy is generally expected to be within .001 inch of a specific profile. Not that you would be able to tell if your bookcase or kitchen cabinet is .001 inch too short, but the accuracy is needed because of other steps in the automated manufacturing process sanding,
laminating, painting, drilling, trimming, etc. If the diamond tool is not extremely accurate, it will have a negative impact on these subsequent operations. The quality of the cut produced by the diamond tool often times has to be high enough that no further processing
is necessary. In other words, a finish cut quality that is good enough to be used for your dining room furniture, right off the diamond cutter. This requires the tool to have various sheer angles, hook angles, conical grinds and multiple piece diamond placement.
All of these technical aspects must mesh together to produce a tool that will cut the profile to within .001 inch of specification without leaving any lines or visible defects.
Because of the fast feed rates, high RPMs are also common with woodworking operations. Routers that rotate at over 20,000 RPM are typical and some profile heads can run over 7,000 RPM. These heads often exceed a weight of 40 pounds, which makes tool runout and balance
very critical issues. It is common to stack several heads on the same spindle to reduce the time it takes to set up for a new profile. This compounds the difficulty and continues to challenge the manufacturers of PCD tooling. Carbide tooling must meet these same challenges
but the fact that the diamond tools are expected to run as much as 100 times longer, makes maintaining the sharpness, accuracy, and balance much more difficult for the diamond tools.
Another major evolution in the woodworking industry is the material itself. When you think of woodworking you are probably thinking of oak, pine, maple- something that comes directly from trees. It might surprise you to learn that the PCD tools we are discussing are seldom
used on these solid woods. The high demand for wood products and the scarcity of good quality natural wood has created a lot of "manufactured wood" materials. In fact, a lot of "woodworking" involves materials that have nothing to do with trees at all.
A more correct term for this industry would be "Resinworking" rather than "Woodworking". It is the resin content, not the wood content, of these materials that has created the need for PCD tools in this industry.
Even traditional woods, such as the oak, pine, and maple, contain resin mixed with the organic fibers of the tree. The resins in these natural woods are relatively soft but they still are the most abrasive part of the natural woods. Diamond tooling is successfully used on solid woods and has proven to be very cost
effective. But the real benefits of PCD tooling becomes much more obvious as the abrasiveness of the material increases. As the amount of resin or the hardness of resin increases in the material being cut, the cost benefits of using diamond tools becomes more pronounced.
Since it is becoming difficult to obtain enough natural wood to satisfy the demand, it is very common to combine a variety of organic fibers held together with resins to create a "wood-like" product. These manufacturing woods not only fill the void in supply, but they have tailored
physical properties that actually exceed those present in nature. The amount and type of resin used has a great deal to do with the physical properties of the material as well as the degree of difficulty during cutting. Some products such as fiber board and particle board contain
ground up, crushed pieces of natural wood, which are combined with a relatively large percentage of hard resin. These fiber boards and particle boards make up the bulk of what is considered the primary focus of PCD tooling in this industry today. Most of your desks, bookshelves, kitchen cabinets,
flooring and many of the other items you thought were made of solid natural wood are actually one of these composite materials covered by a very realistic looking woodgrain laminate.
One of the new concepts becoming popular today is to create a wood type product that is about as far removed from the forest as you can get. Today, many materials that are used for making furniture, kitchen cabinets, and floors appear to be wood, but have no wood in them at all! These materials
(such as wheatboard and strawboard) are made from organic fibers left over from agricultural processes mixed with various types of resins. So when you are at home admiring what you think is a solid wood bookcase, keep in mind that what you are really looking at is "cattle feed" mixed
with resin and laminated with a paper overlay that looks like an oak grain. If tungsten carbide tools were used to cut these highly resinous materials, the short life of the tools and frequent tool changes would make it very costly, not only in tooling but in machine down time due to
constant tool changes.
The furniture makers of today are vast, automated, computer controlled worlds that have millions of dollars invested in single machines which have to be run day and night to generate favorable payback. They bring train loads of raw material (MDF, particleboard, etc.) into one end of the building
and the material is continually processed into finished goods- often never being touched by human hands. The machinery is connected together in "production lines" and the product never stops moving until it is put in shipping boxes and loaded on trucks at the other end of the building.
If one piece of machinery has to be stopped to change dull carbide tools, the entire production line generally has to be slowed down or even stopped. This represents millions of dollars in equipment that is setting idle because of short tool life. You can imagine the benefit of using longer
life, diamond tooling when it eliminates 100 tool changes that would occur if carbide tools were used. PCD tooling may be 20X the price of carbide tooling, but if it runs 100X as long, it doesn't take much time before the benefits of increased production rates and decreased
downtime more than cover this cost difference. Most furniture manufacturers have realized that if you put a $50 carbide tool on a $1,000,000 piece of machinery, you get $50 performance!
As we look at other materials that are even higher in resin content such as synthetic stone, Corian, Formica, plastics, fiberglass, acrylics, Kevlar, etc., we can see where the term "woodworking" is much too narrow of a definition for this industry.
It is the amount and type of resin in these materials that drives the equation toward the use of PCD; and some of these materials are pure resin. Many of these compounds can not even be cut without the benefit of the hardness and abrasion resistance inherent in diamond.
A relatively new application for PCD tooling, that is considered part of this same "woodworking" market is the manufacture of "cement board" such as HARDYBOARD and FORTABOARD. This material is widely used in the Far East and is becoming increasingly popular in North America. It
is used for housing construction and has the appearance of wood siding but is made out of a mixture of wood fibers, gypsum, resin and concrete. In this case, it is not only the resin content but the gypsum and concrete in the material that causes the problem. You can't get much further away from natural
wood than this product. These cement board sections must have a tongue and groove type joint cut into them and this is done with very large diamond tipped cutter heads. Even with the most abrasive resistant, coarse grain PCD, a tool life of 2-3 days is the maximum you can expect when cutting this
material. Anything less than diamond will not even scratch the surface.
Another challenge faced by the tool maker is that several different types of materials may be combined or layered to achieve the right combination of physical and cosmetic characteristics. You may have a particle board center with a hard Formica type material on top and a soft paper or plastic on
bottom. Therefore, in one single cut, the tool has to deal with a very hard surface overlay, a medium tough and abrasive core and finally a very soft, easily frayed material on the bottom. This necessitates a single tool that has three different geometries and possibly three different types of PCD
along its cutting edge. Some of the combinations can get very bizarre as manufacturers try to combine cosmetics with stain resistance, water resistance, fatigue strength, thermal insulation, impact resistance, light weight, scratch resistance, etc.
One of the more extreme examples is the hard surface laminate flooring which is popular in Europe and gaining more of the market in North America. This material actually has a very hard aluminum oxide overlay to prevent scratching of the flooring. Under the aluminum oxide is a paper overlay that has a
wood grain appearance. The core material is usually fiberboard and the bottom layer is heavy paper. Tooling to cut this material effectively requires combining PCD with single crystal diamond to get the optimum tool performance. The single crystal diamond is needed because the abrasiveness of the aluminum
oxide overlay is too much for even the PCD to handle.
Some other examples of material combinations, often encountered in this industry are shown below. Keep in mind that all of these fall under the domain of "PCD Tools for Woodworking" and virtually no wood exists in any of them.
![]() Fiberglass for boats, snowmobiles, recreational vehicles | ![]() Bullet proof glass and composite fibers for military and commercial aircraft |
![]() Plastics and acrylics used for display cases and store fixtures | ![]() Composite materials used in snow skis, water skis, skateboards, and hunting bows |
The common thread in the success of PCD in these markets is that the tool manufacturers have been very open minded to new market opportunities. Sometimes we seek them out and sometimes customers thrust these challenges on us. Either way, we aggressively pursue these opportunities. We know that there are new types of PCD coming onto the market as well as improved types of equipment that we can use to get better tolerances, improved finishes and more complex geometry on the tools we make. Our experience and techniques are being honed and we are becoming better armed each day to tackle these new challenges.
We consider ourselves generalists, not specialists. We are not in the woodworking, plastics or metal working business. Even the new term "Resin Working" discussed earlier is still too narrow to cover what is being done. We consider ourselves in the Chip Making Business- if you can cut a chip out of the material, we can make a tool for it. The only limit we put on ourselves is: "if diamond, the hardest material on earth can't cut it, we back away." Anything else is considered part of the market or represents future growth potential for PCD tooling products.